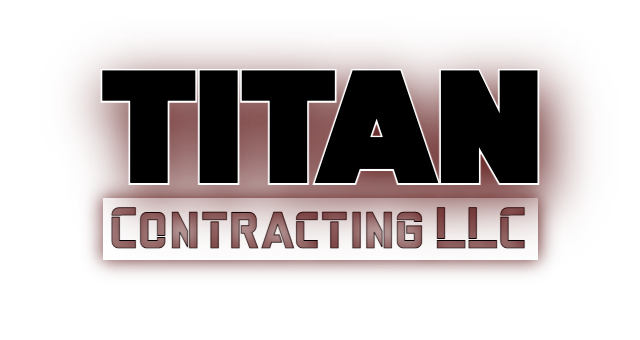
Our Goal
The goal is to increase the concrete cycle life and seal all concrete rails and decks which do not have a dense overlay and are in deck condition states (CS) 1 and 2 on a four to seven year rotating schedule, depending on the type of sealer applied. Decks in CS 3 should be crack sealed prior to applying a deck slant and those in CS 4 and CS 5 should be brought to CS 2 or 1 prior to deck sealing.
This is a four Year cycle on all concrete decks
Purpose of sealing concrete Decks and Railings
Sealers are used on cement concrete decks and railings to reduce the rate of chloride attack on the reinforcing steel, thereby extending the service life and reducing life cycle structure costs of the deck. Additionally, by reducing moisture in the concrete, the severity of freeze-thaw deterioration and spalling due to rebar corrosion, is reduced.
By applying sealers to existing concrete surfaces, the permeability of the concrete is reduced by up to one order of magnitude. The permeability of the concrete is one of the most important factors which will affect the rate of deterioration of rebar corrosion, alkali-aggregate reaction, carbonation, and the effects of freeze-thaw cycles. All of these can occur simultaneously. Even on dense concrete overlays, sealing small and micro cracks will prevent intrusion of water and chlorides.
History of Concrete Decks and Bridges
One county in Wisconsin has reported more than a 60% reduction in deck-spalling after four years of their program using Siloxane sealers on concrete decks, which do not have dense overlays, using both a two year (for county bridges) and four year reciting cycle (for state bridges). Alberta’s Ministry pf Transportation has 19 years of continuous use of Silane sealers and reports extended life on their dense concrete decks using a three year coating cycle. Montana and South Dakota have been using Methyl-Methacrylate crack sealing with reported good success in extending the life of their bridge decks.
Types of Sealers
Penetrating Sealers: Penetrating sealers are products that are absorbed onto the surface of the concrete and react with the concrete to form a hydrophobic ( water repelling) surface. The pores and cracks in the concrete are not blocked and while liquid water is repelling water from all the surfaces
- Silanes - Low molecular weight penetrating sealer, which allows for maximum penetration of pores and fine cracks. Silane has excellent vapor transmission properties.
- Siloxanes - Higher molecular weight penetrating sealer which has about half the penetrating ability of Silane. It has good vapor transmission properties. (Suitable for sealing less dense concrete and coarser cracks.
Polymer Coatings: Polymer Coatings (colored or clear) are products that bond to the outer surface of the concrete and form a film. The water proofing properties of the coating are generally independent of the concrete, although adherence to the concrete is necessary for the coating to function.
- Methyl-Methacrylate - Of higher molecular weight than Siloxane, it has good crack penetrating properties, but fills rather than coats pores and so has poor vapor transmission. The coating is rapidly removed from wearing surfaces and relies on its penetrating ability rather than sealing the concrete surface. To provide water proofing ability. A blotter seal is usually applied to remove surface residue and provide friction for traffic. Caution: use high molecular weight methyl-methacrylate to reduce flammability. Best application is for extensive fine cracking.
- Epoxy - Penetrating abilities vary by product, but primarily is used to provide a barrier coating to ingress of water. Most exposes designed for use as a deck sealer have good elastic properties to span and cover cracks as they move. Some epoxy sealers are formulated to also have good penetrating capabilities. When applied in traffic areas, epoxies are always applied with additional friction materials, usually an aggregate chip.
Selecting Concrete Sealers
Sealer service life
Service life is dependent on the specific manufactured product, the application of the sealer, ands the severity of service it enoerienvces. The following ranges assume good application and for polymer and bituminous coatings, low to moderate traffic levels.
Penetrating Sealers | Polymer Coatings |
---|---|
Silanes 3 to 5 years | Epoxy - 10 to 20 years |
Siloxanes - 3 to 5 years |
Condition of Concrete Deck
Condition State 1:
Deck has little or no deterioration ( no notable spalls, delaminations, or patches). The wearing surface may have superficial cracking, scale, or wear. The underside of the deck may have isolated leaching cracks, but there is no notable rust staining or water saturation.
- Seal using ReShield-40 or RepProtect AC every four years
- Option: Use Siloxane on concrete decks without dense overlays.
Condition State 2:
Deck has minor deterioration (isolated spalls, delaminations, or patches) - the percentage of unsound deck is less than 2% of the total deck area. The wearing surface may have minor cracking, surface scale, or wear. The underside of the deck may have minor leaching cracks - there may be isolate water saturation or rust staining.
- Seal using Silane every four years.
- Option: use Siloxane on concrete decks without dense overlays.
Condition State 3:
Deck has moderate deterioration ( spalling, delaminations, or patches). - the percentage of unsound deck is between 2% and 10% of the total deck area. No full depth failures are present. The wearing surface may have cracking, surface scale, or wear. The underside of the deck may have leaching cracks, water saturation, or rust staining.
- Crack seal before deck sealing with Silane or Siloxane, or Crack seal using Methyl-Methacrylate and sand blotter. (Best application is for decks with many cracks.)
Condition State 4:
Deck has extensive deterioration ( spalling, delaminations, or patches) - the percentage of unsound deck is between 10% and 25% of the total deck area. Isolated full depth failures may be present (or imminent) - structural and underpinning may be required. The wearing surface may have extensive and significant cracking or scaling. The underside of the deck may have extensive and significant leaching cracks - there may be extensive water saturation or rust staining.
Condition State 5:
Deck has severe or critical deterioration. The percentage of unsound deck is greater than 25% of the total deck area. Full-depth failures or impending failures may be prevalent. Immediate structural underpinning may be required. Wearing surface may have severe spalls requiring immediate repair.
- Repair prior to sealing deck
Maintenance Life Cycle

- Inspections consists of: Decks, Columns, Beams, & Spandrels
- Deck Inspection for: Spalling, Cracking, & Delimitation
- Drainage Inspection consists of: Leaking, Clogged Drains & Adequate Drainage
- Inspect for exposed Steel for distress
- Visually Inspect Bearing Pads, Expansion Joints, & Header Joints
- Safety Inspection Consists of: Slip & Tripping Hazard, Handrails, Landings, Cable Barriers
- Repair where needed:
- Cracked Concrete by injection, patch or sealer
- Add strength to structures with Carbon Fiber, Epoxy
- Spalled Concrete - saw cut, remove broken concrete, patch
- Maintain / Preventative
- Methyl Methacrylate Epoxy Re-bond concrete stop spalling & cracking also waterproof coatings.
Why Maintenance Matters
In most cases a maintenance program will extend the service life of a structure increasing the owner's return on investment and decreasing liability.
Our maintenance program follows the Amercian Concrete Insitute's Code 562 Code for Assessment, Repair & Rehabilition Of Existing Concrete Structures. ** Local Codes Are Also To Be Followed By ACI Code 562
With Structures showing deterioration the first step in the Assessment Phase will be a Licensed Professional Engineer inspecting the structure then issuing the owner a report.
Structures not showing deterioration such as a newer structure needing a maintenance program for water proofing decks and joints, a concrete healer sealer, or a minor repair along with our experience and knowledge we work alongside our trusted suppliers to get the right fix needed in each case.
A maintenance program depending on the condition of the structure might entail a multi-year program depending on the Engineer's assessment and report. This is where Titan Contracting can be a trusted partner in this process taking care of your structure.
What is Epoxy Concrete Injection?
Injection is a procedure of pumping cement-based, polyurethane-based, epoxy-based or acrylate-based material into damaged or cracked structures to securely seal leaks, repair compromised structures and make them watertight again for the long term.
Epoxy injection is the process of injecting an epoxy resin into cracks to essentially glue the concrete back to its original state. It is an economical way to restore cracked concrete slabs and walls back to their original structural design.
It doesn’t help either that cracks in concrete are almost inevitable. At best, these can be just an unattractive nuisance. At worst, they lead to leaks that can damage the interior of the building, corrode steel reinforcements, and ultimately shorten the life of the concrete structure. Even if concrete cracking does not affect structural performance, it can adversely affect the durability of structures by allowing chloride or carbon dioxide deep into the structural element and initiating corrosion over time.
TuffTex Crack Injection System
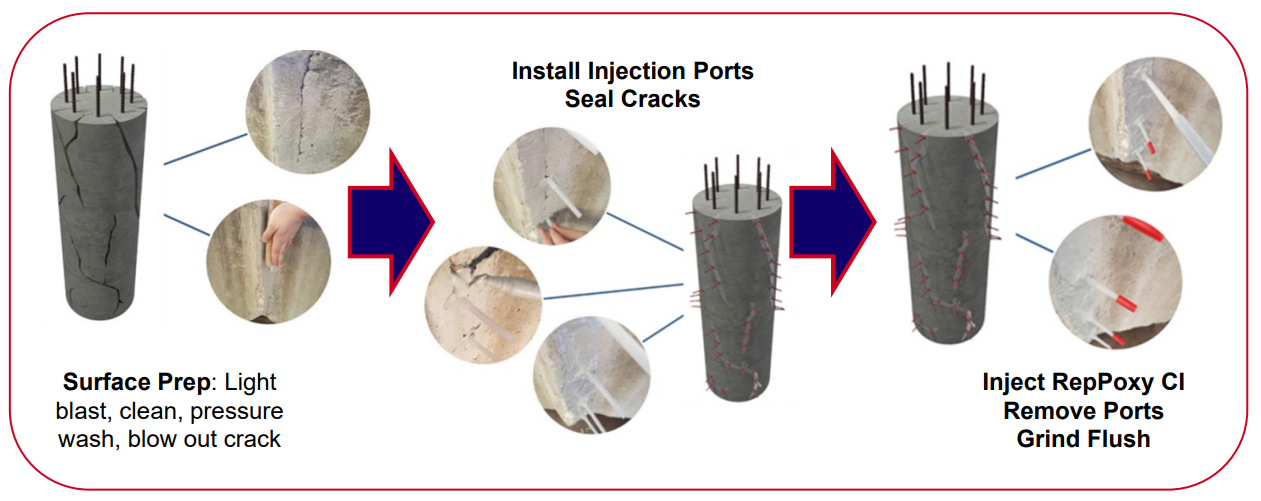
Joint Sealing
Joint sealing is an essential step in maintaining concrete structures, such as parking garages, concrete buildings, and sidewalks. Expansion joints between sections of concrete strategically control where cracks occur in the concrete. These joints need to be sealed to work effectively. Also It's important to seal the joints because this keeps water, ice and dirt from seeping into the concrete and freezing causing potential heaving and corroding rebar and or causing more deterioration of concrete
Concrete Spalling
Concrete Spalling is the breakdown of concrete via natural weathering and/or chemical reaction that results in sections of cement chipping off the main body – often resulting in fractured, compromised or unconsolidated concrete. Spalling looks like pitted scarring and breaks off which can expose rebar and comprise the rest of the concrete structure. Waterproofing or Sealing the concrete is the best way to prevent moisture-related spalling.
Carbon Fiber Strengthening System
Using carbon wrapping for columns reinforcing bars in new concrete can eliminate potential corrosion problems and substantially increase a member’s structural strength. Carbon wrapping for columns this strengthening technique causes minimum disturbance to the structural members as compared to conventional methods. Carbon wrapping for columns is resistant to corrosion; hence they are used for corrosion control and rehabilitation of reinforced concrete structures.
Carbon fiber has very high tensile strength and is also very lightweight. When bonded to the exterior of a concrete column, beam, or slab, it can add significant strength without adding weight that would increase the load on foundations and other structural members. The composite material is called fiber-reinforced plastic (FRP). FRP wraps are easy to apply and can be used on any size or shape of structural member. Traditional techniques for strengthening, such as adding concrete and reinforcing steel around the outside of a structural member (often with shotcrete), external post-tensioning, or adding structural steel supports shoring often are more expensive due to the extra work to get everything into place.
- Carbon Fiber Wrapping System provides tensile strength
- It offers high in chemical resistance
- It is temperature tolerant to excessive heat
- It offers low thermal expansion
- Adds strength to concrete
- Increases load carrying capacity
- Restoration of damages structures
- Elimination of corrosion problems
- Effective in bending and shear
- Protection from environment elements
- Replace damaged or missing reinforcing steel
Paver Restoration
First Coat of restoration and Sealing, : These Pavers were only installed 13 months ago. The concrete in pavers will fade if not sealed
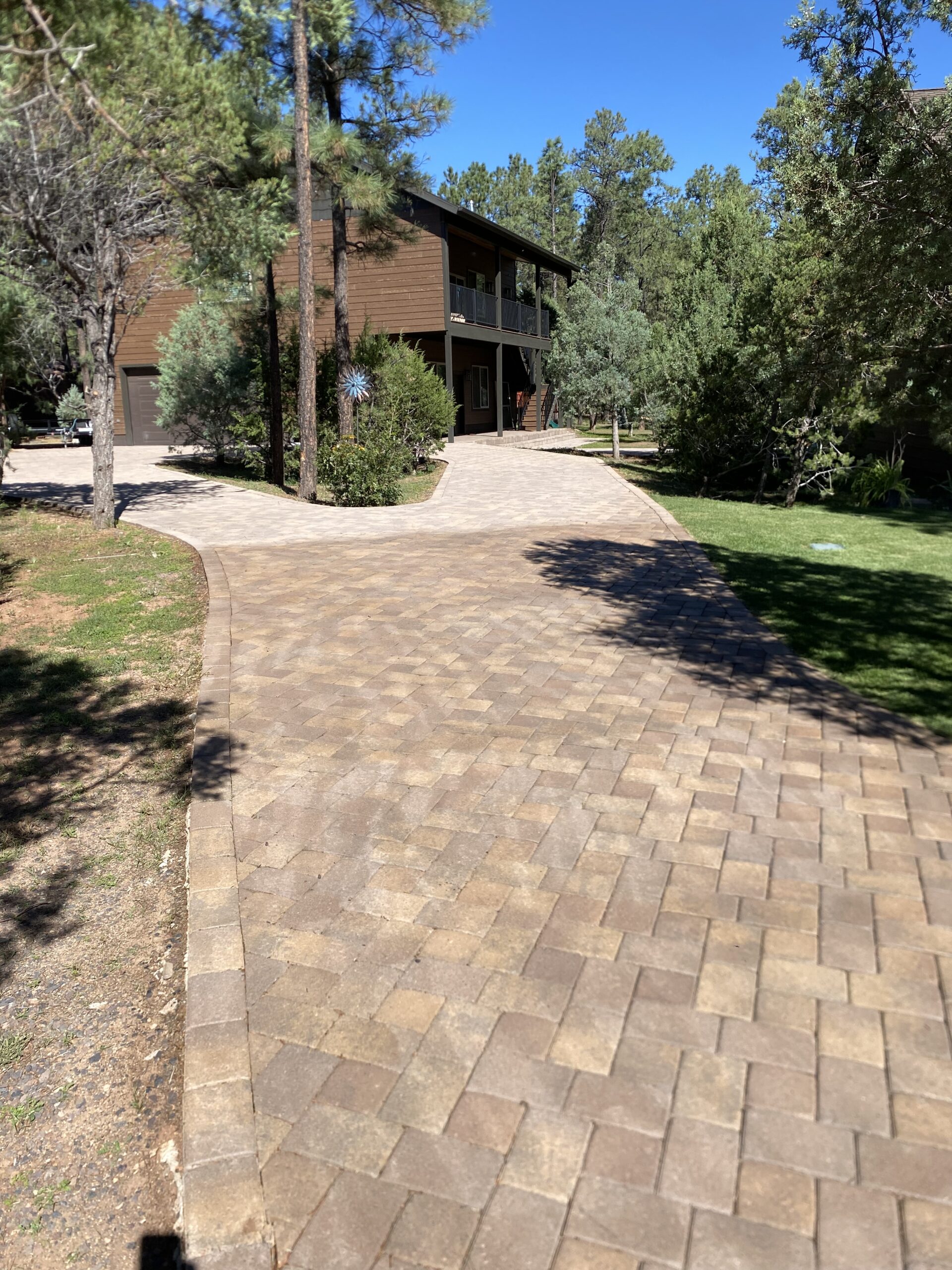
Notice pavers covered out of natural weather conditions have not faded as bad as uncovered pavers, pavers were only installed 13 months ago
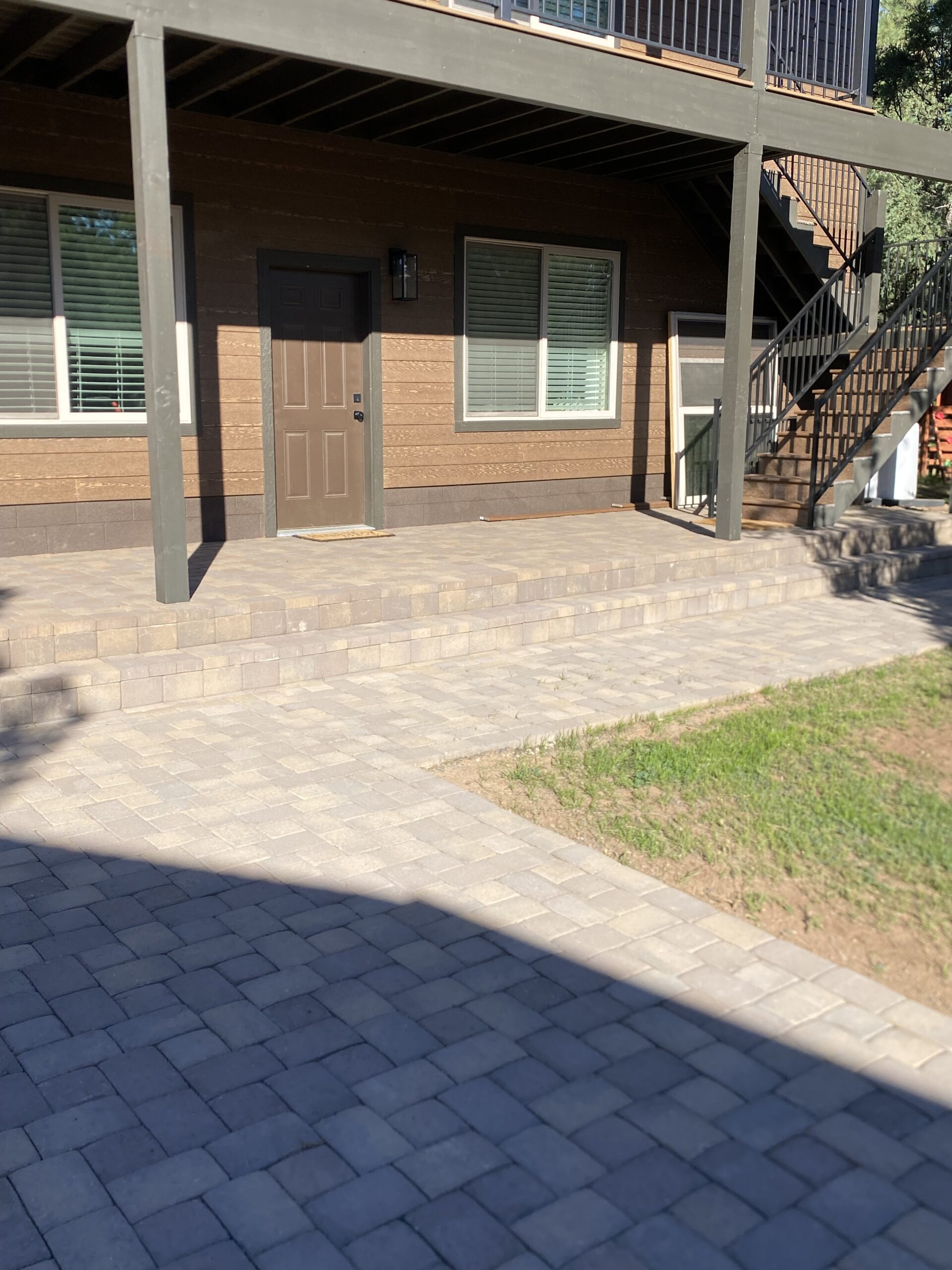
We can adjust the sheen on final coat, this customer just wanted to the natural colors back and a low sheen
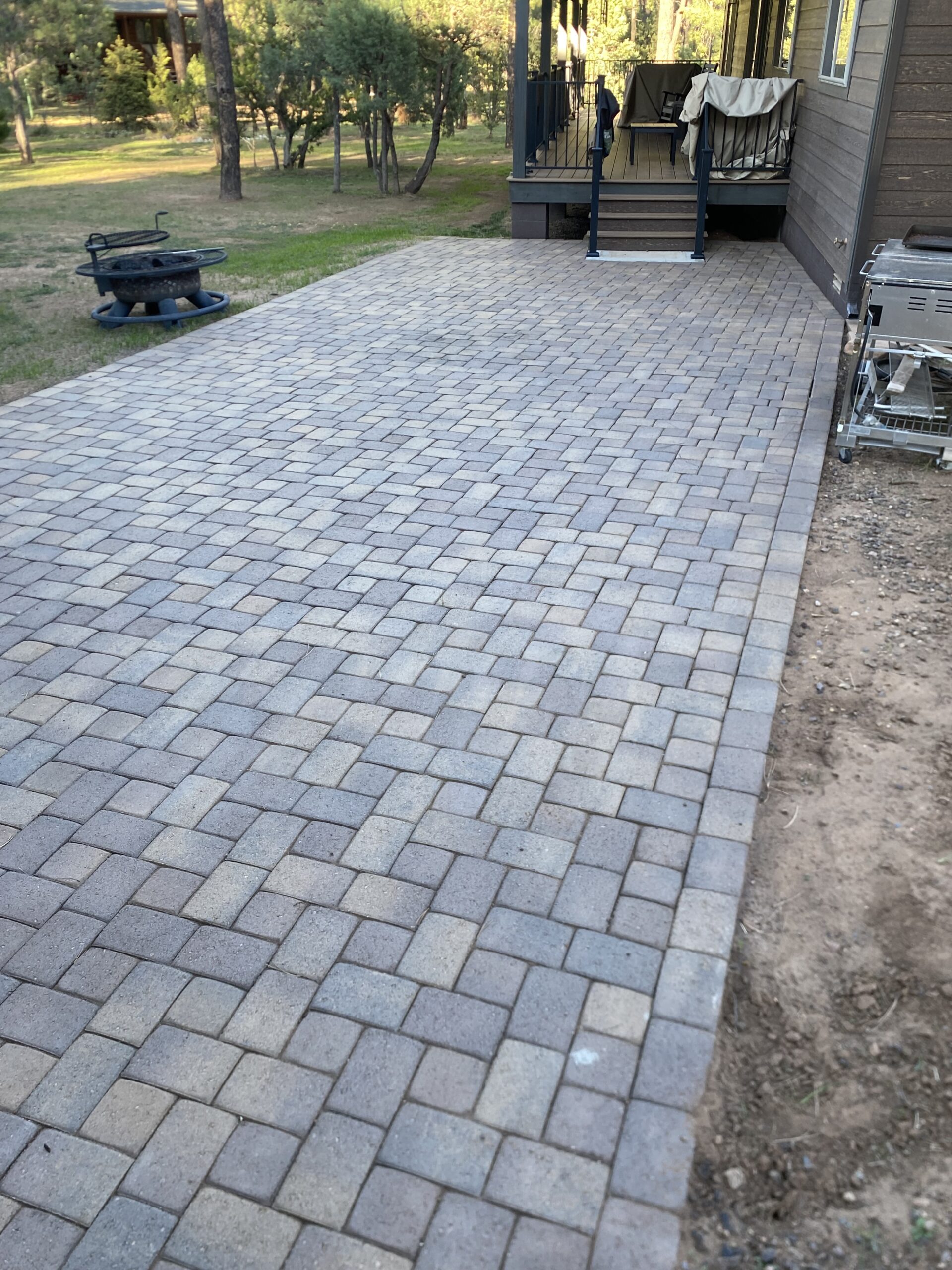
1st Coat
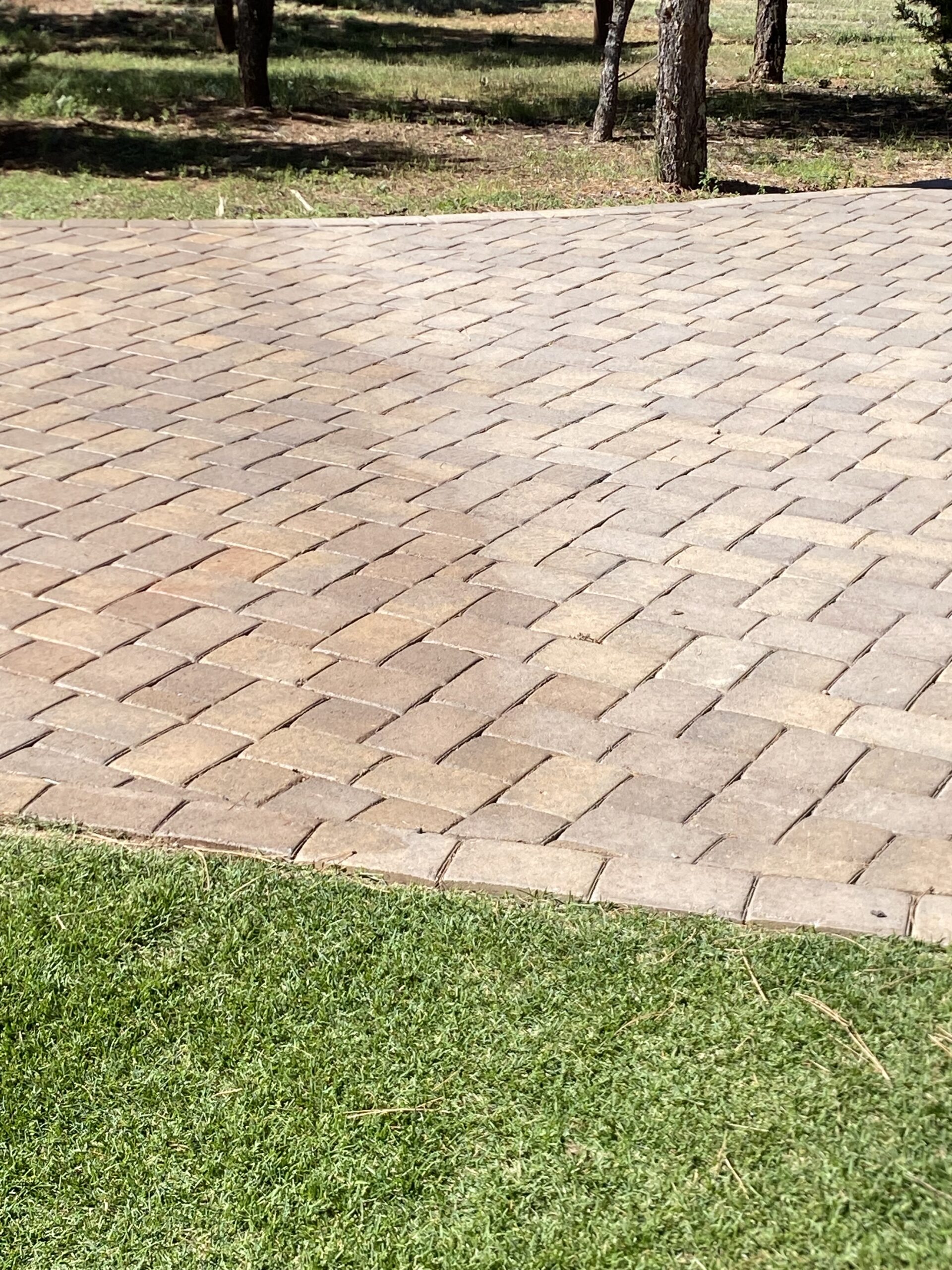
Natural Color restored
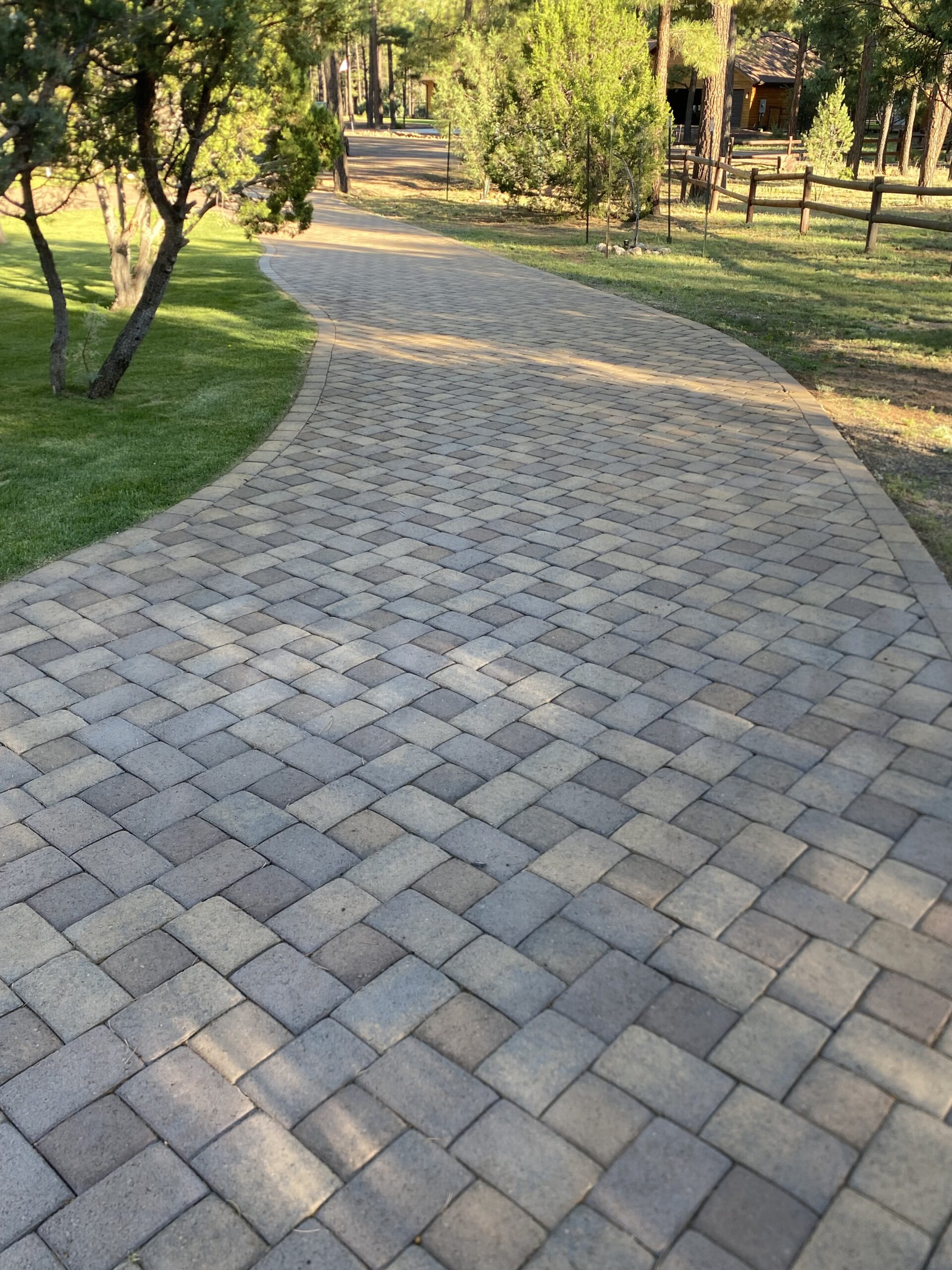
Titan Epoxies
We use machines not chemicals to grind high spots and remove any foreign substances for better bonding
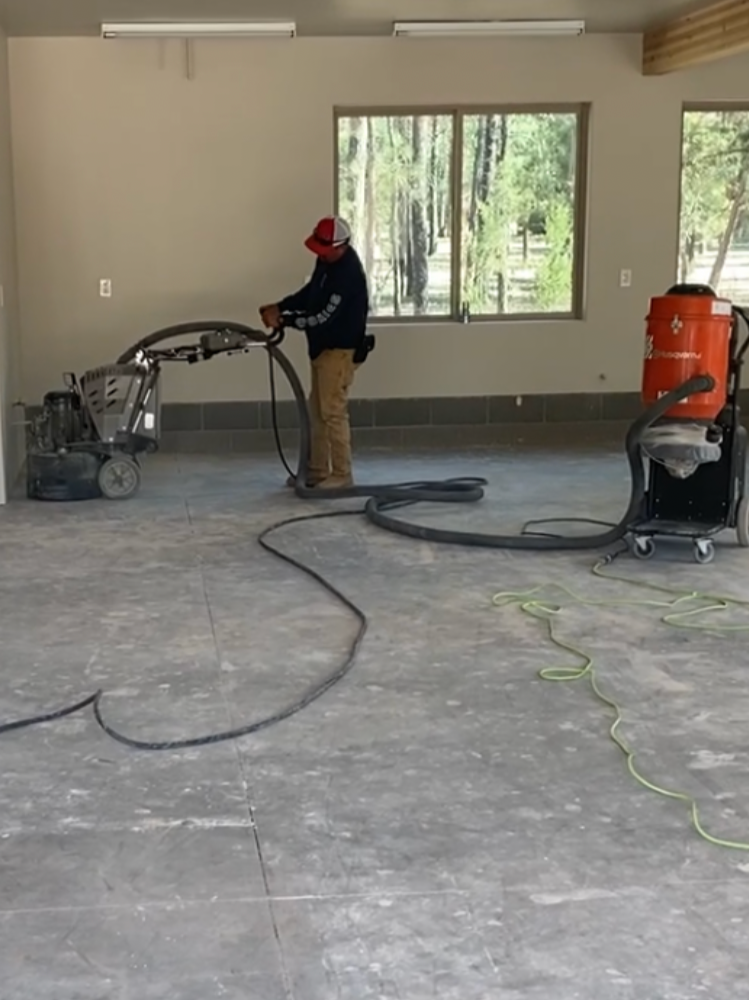
Metallic Epoxy Floor
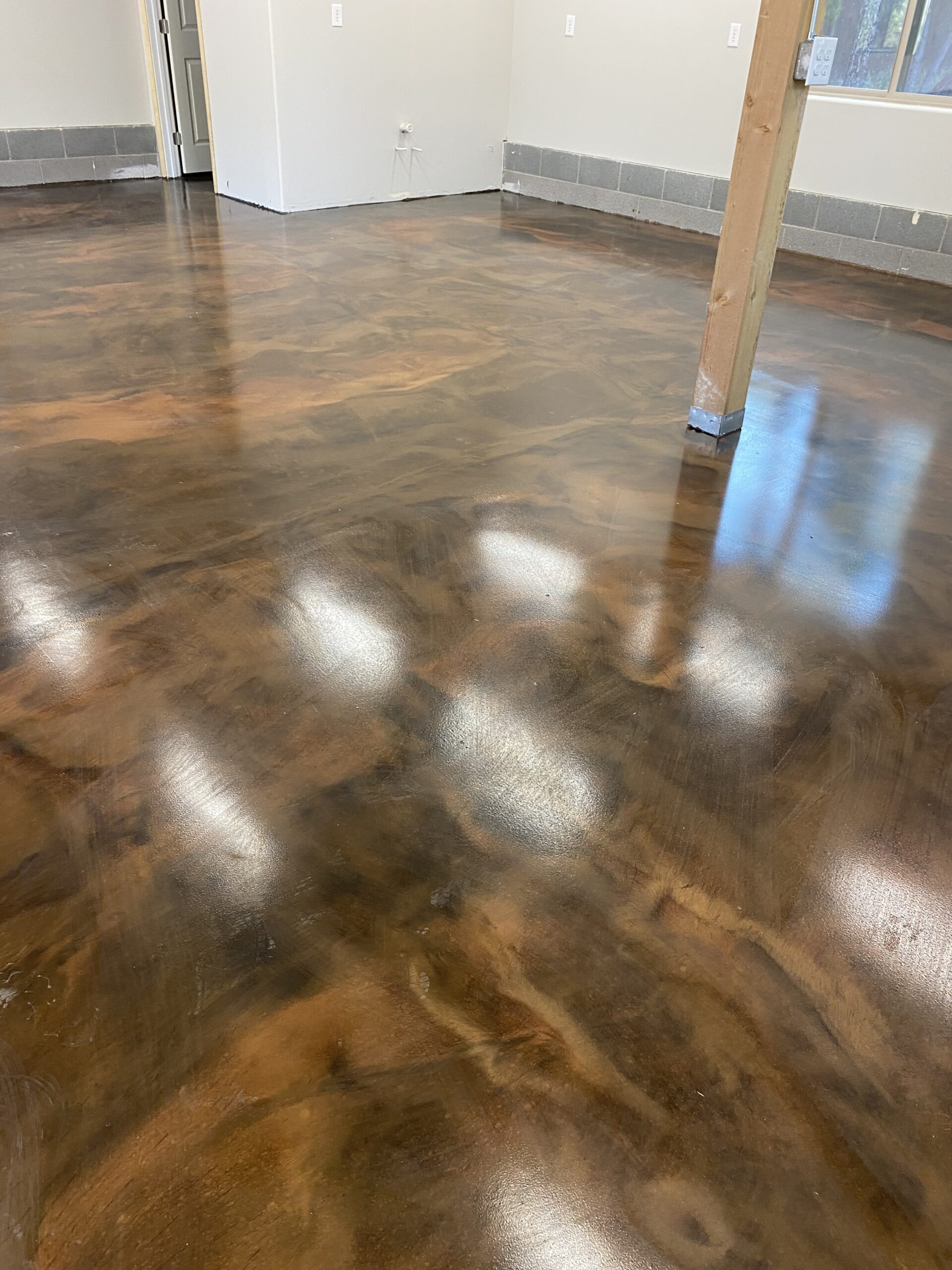
Concrete Staining New or Old Concrete
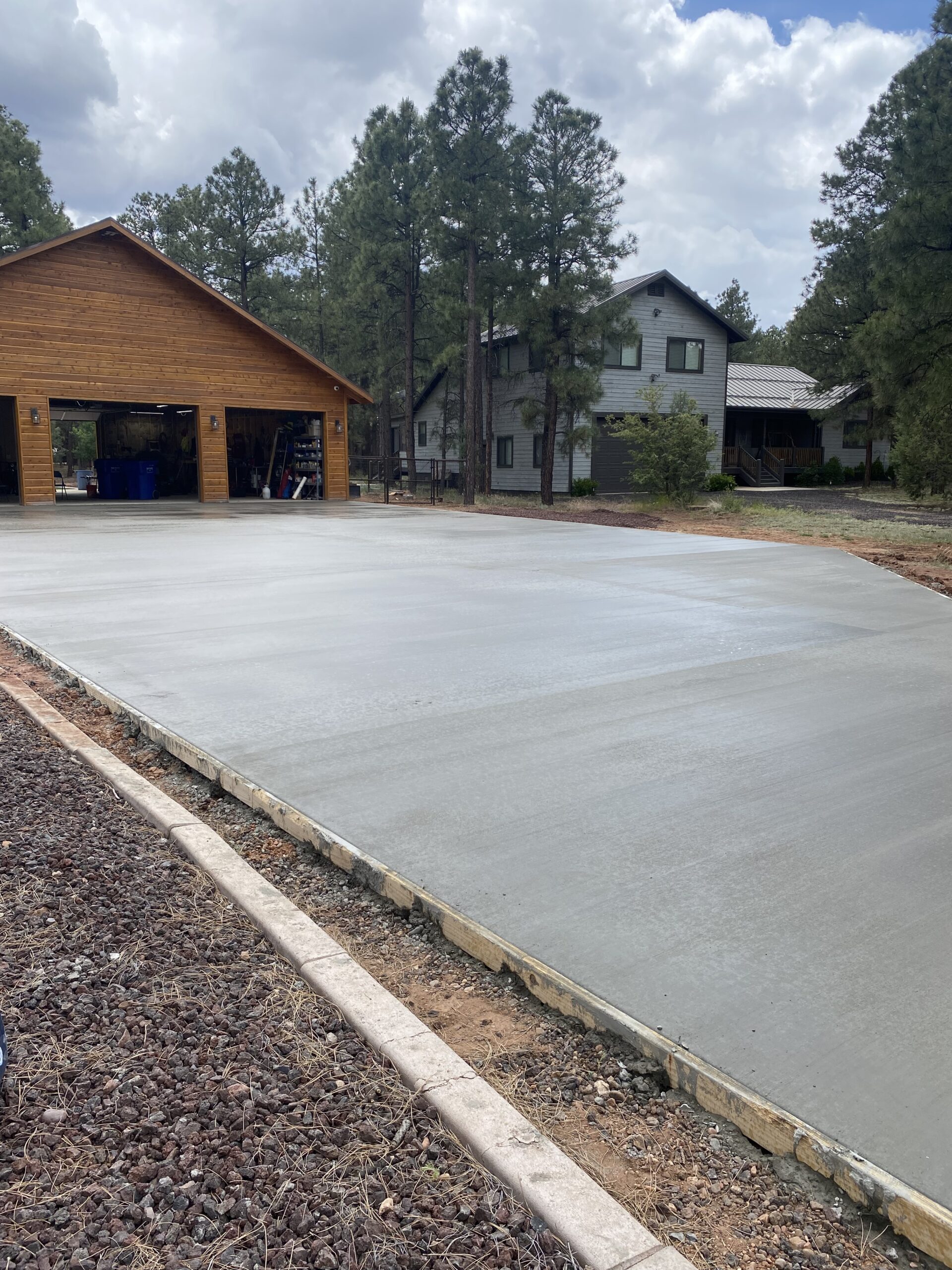
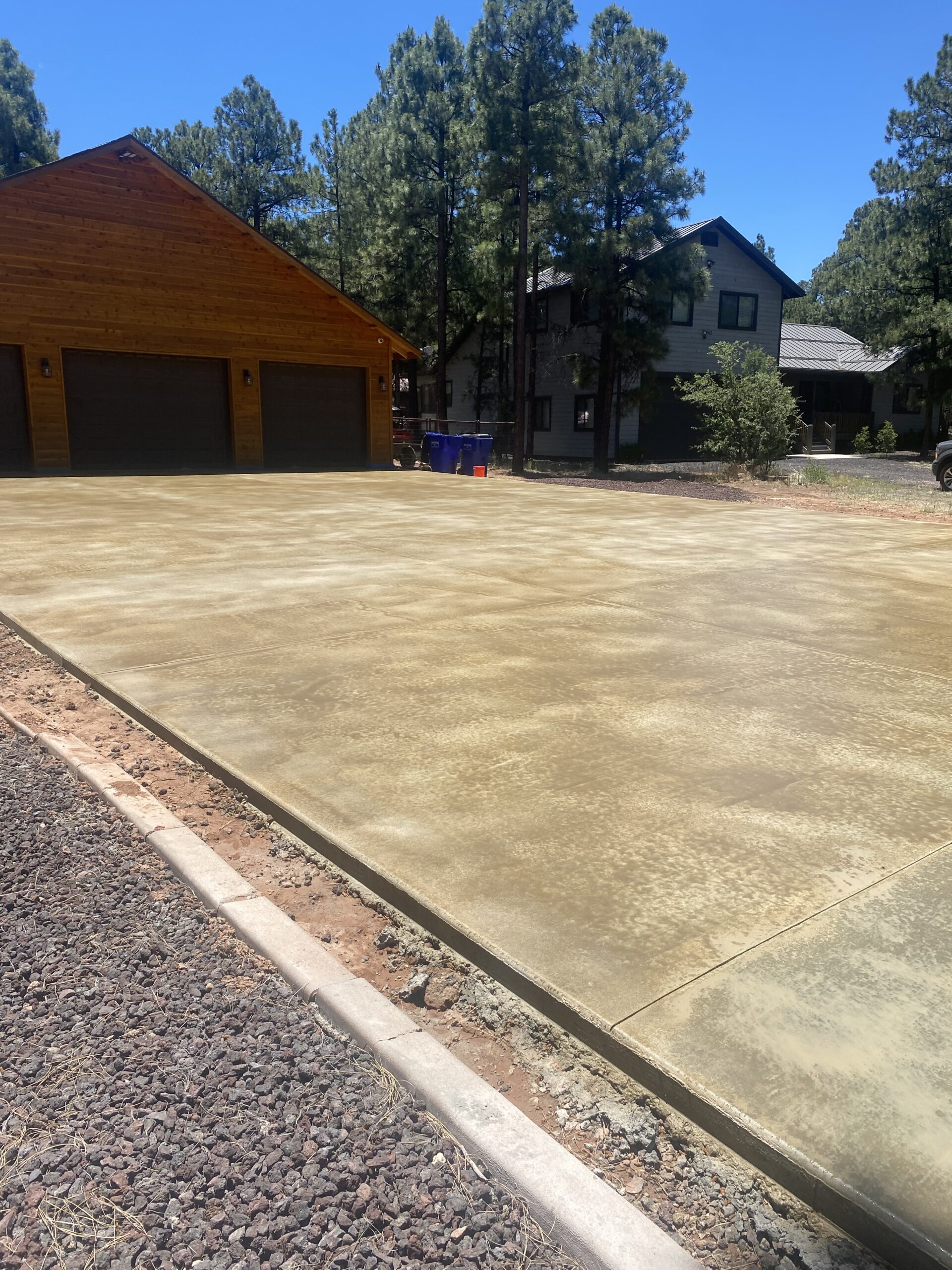
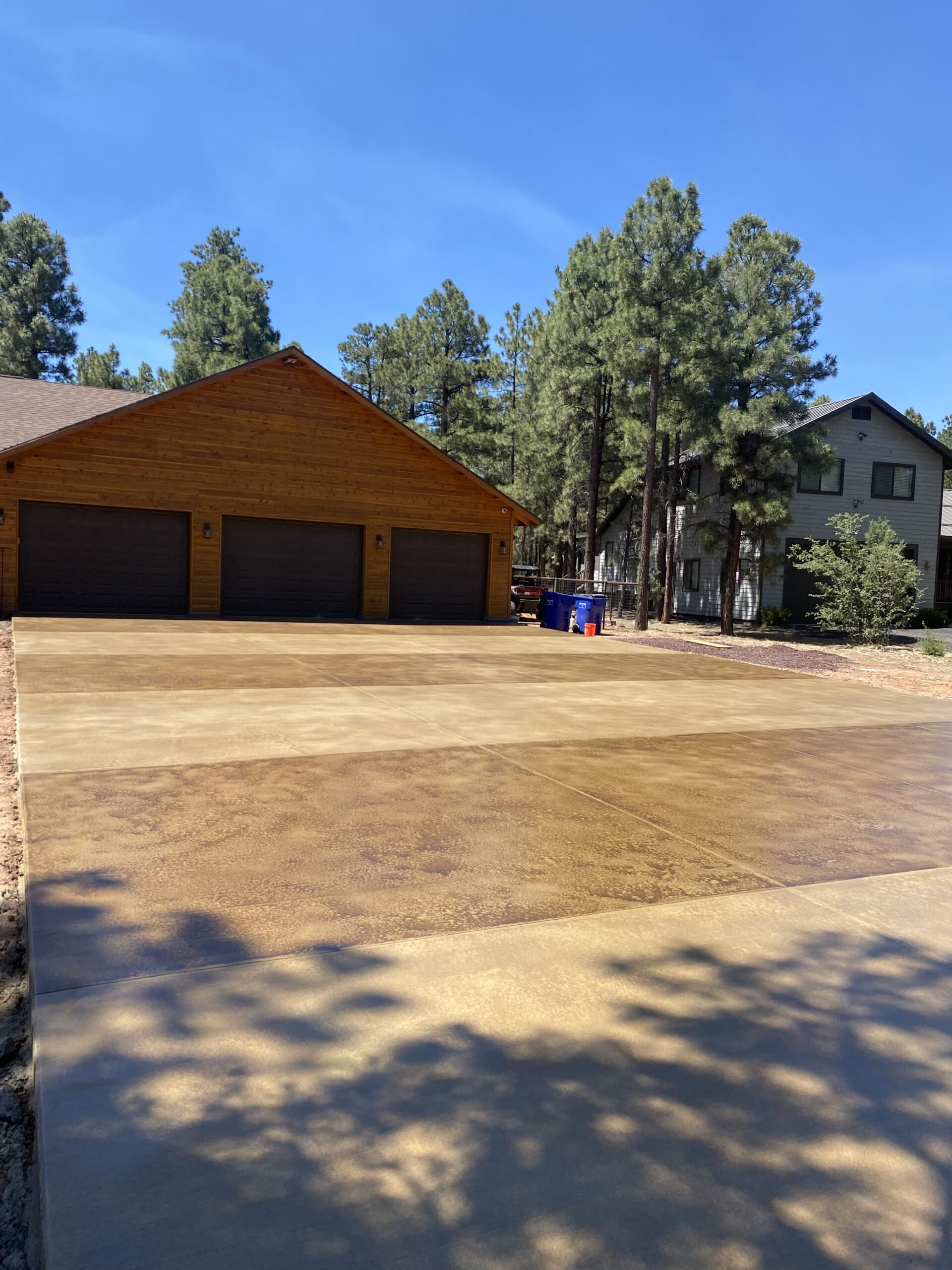
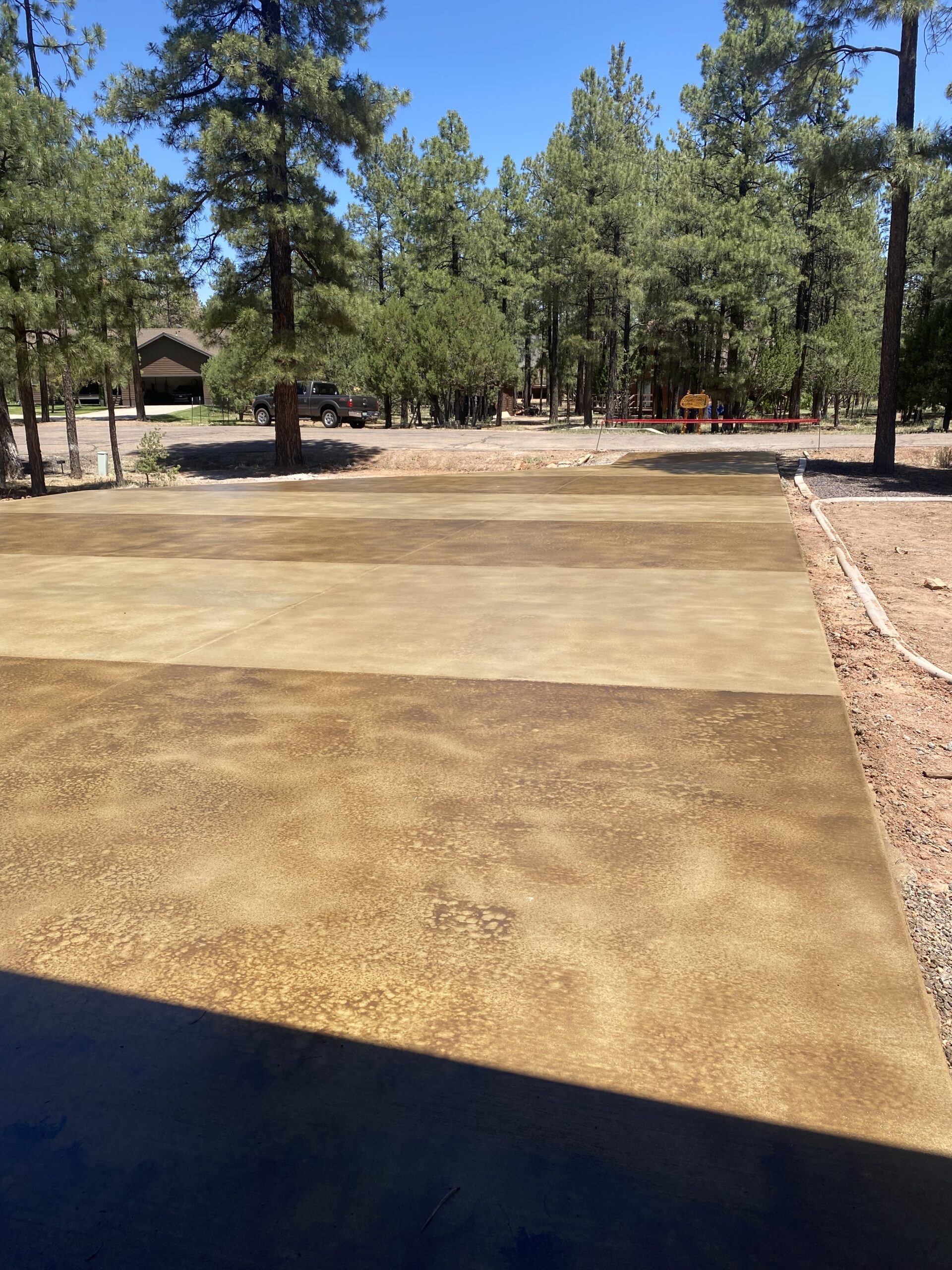
Prep For Epoxy Flake Floor
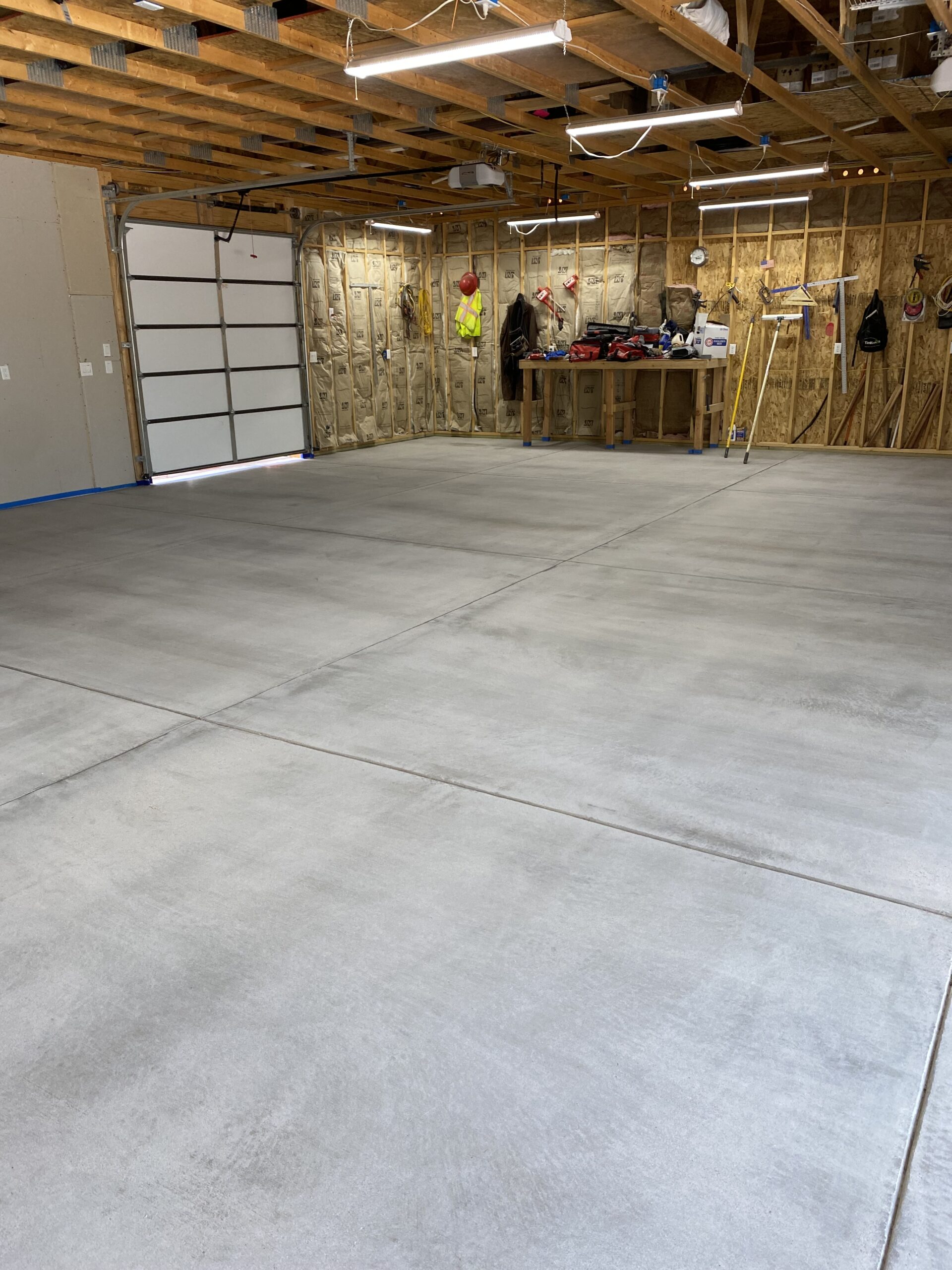
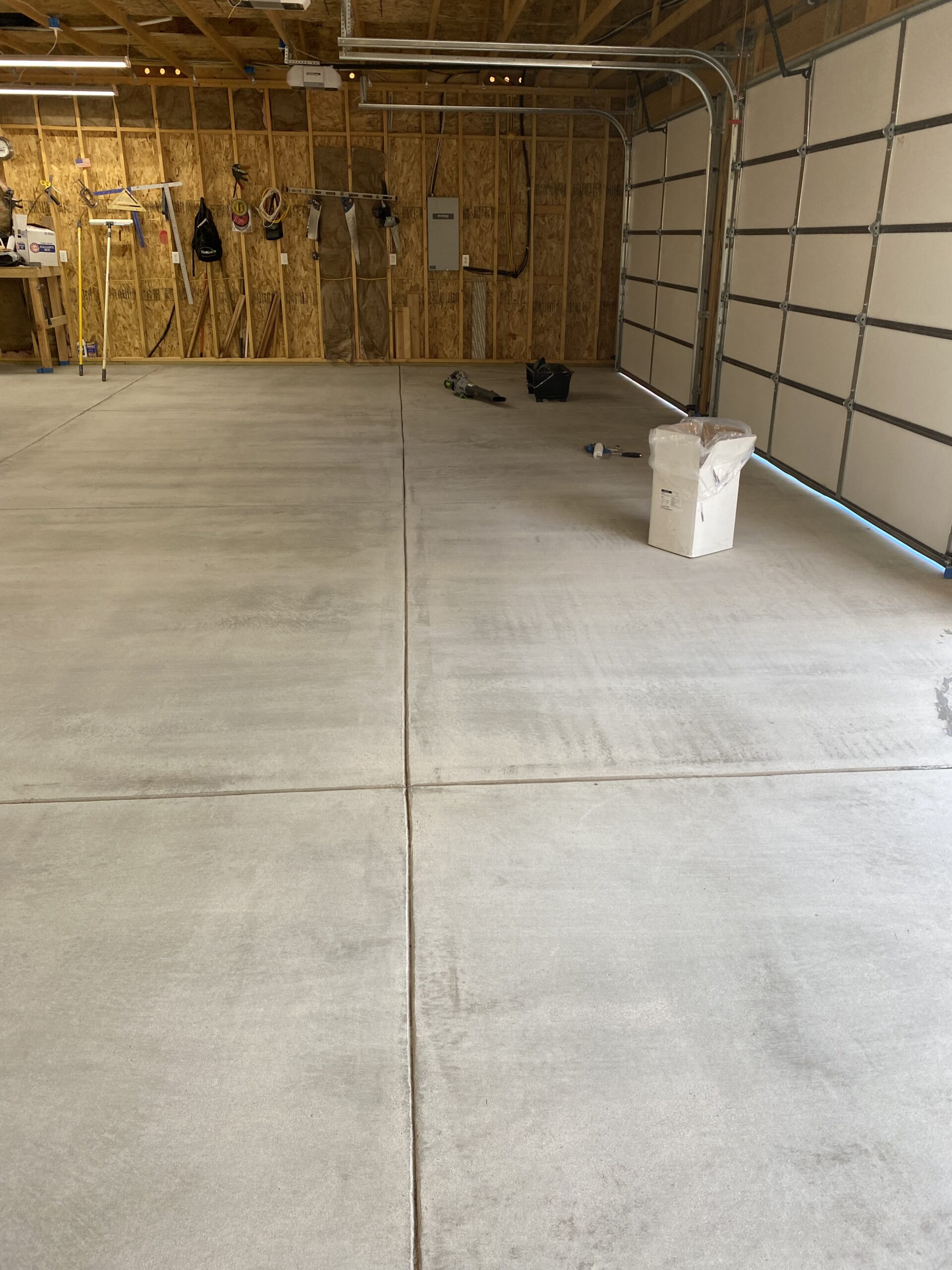
Epoxy Flake Floor
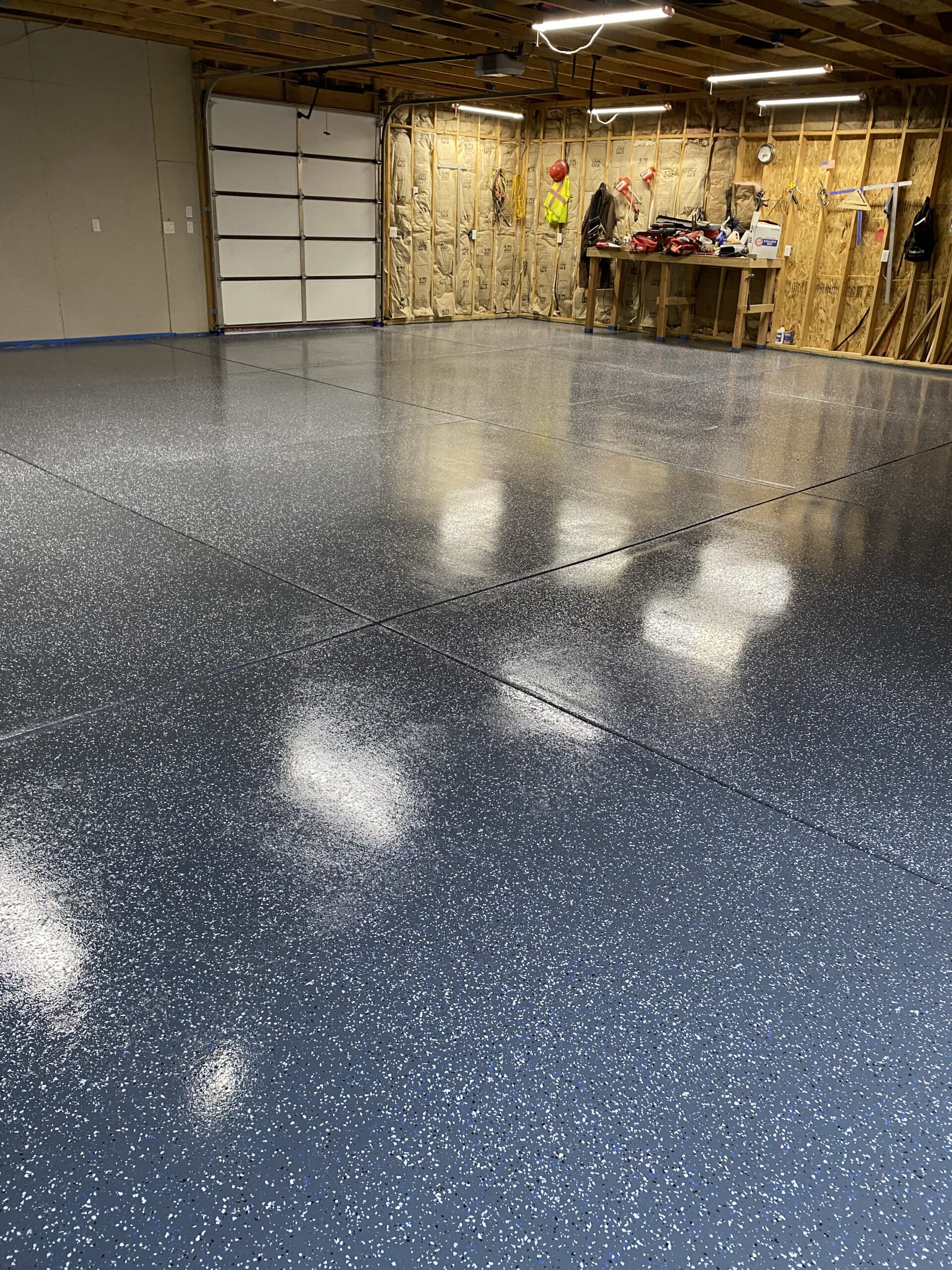
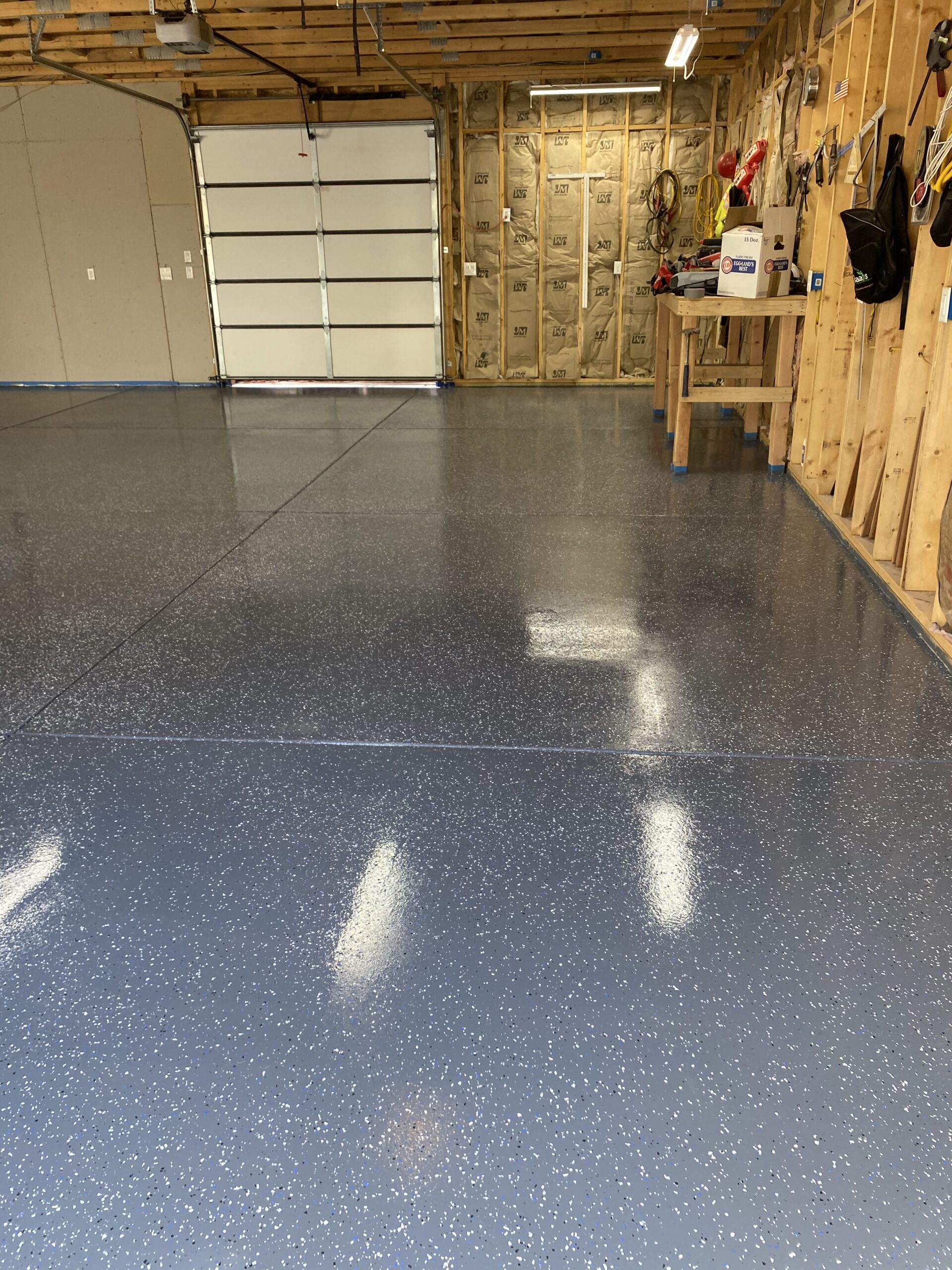
Old Discolored Concrete
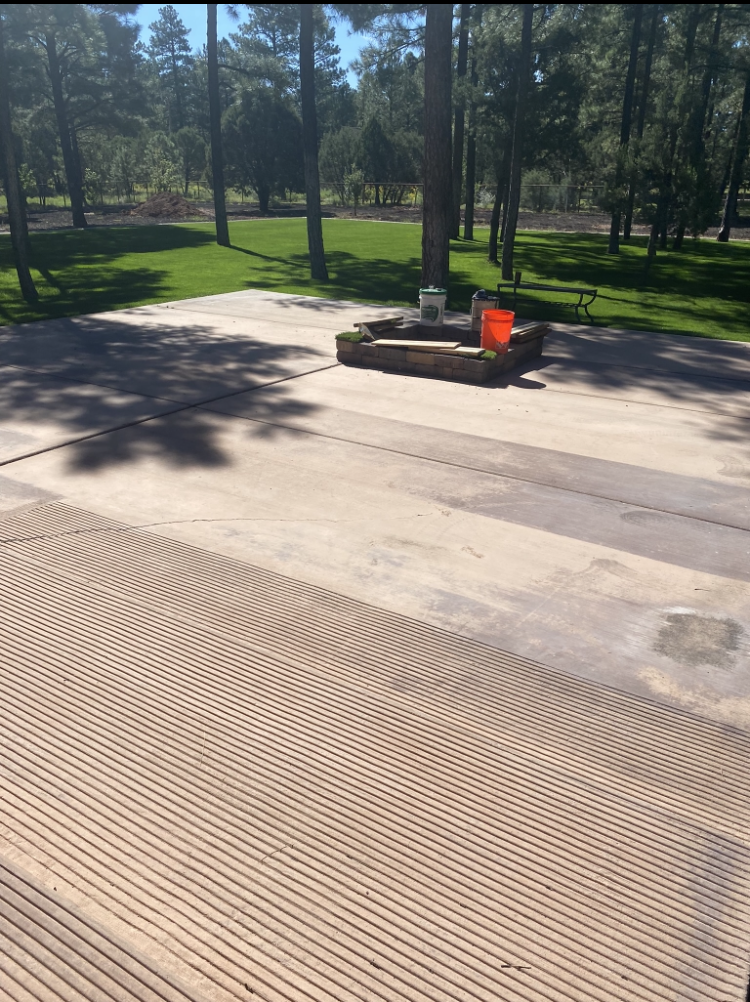
Restored and Sealed
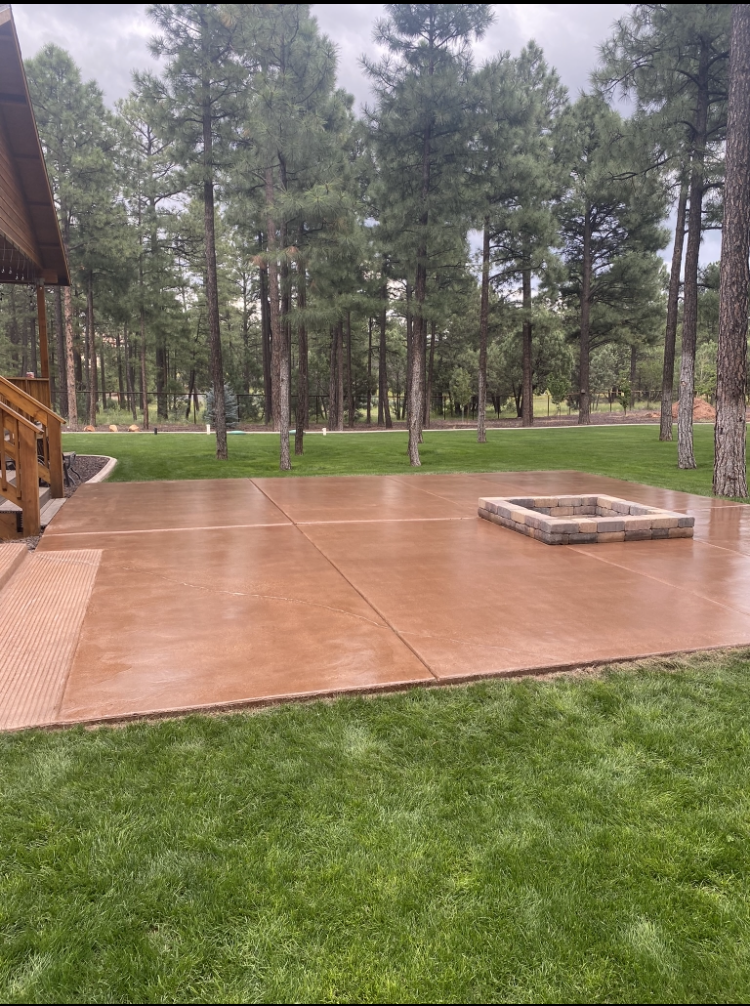
For More information: Please Contact Stacey at 928-379-9580
About Titan Contracting
With over 30 years of experience, you can trust Titan Construction with any job, no matter the size or difficulty. We pride our self on dependable estimates, top of the line production, and on time completions.
- Arizona A- General Engineering License
- Arizona CR- 9 Commercial & Residential Concrete
- Utah A- General Engineering License
- Texas- TXDOT Approved For Carbon Fiber Repairs & Concrete Repair Concrete Structures
Experience You Can Trust
Bill Kerr Professional Experience
Kerco Companies (1985-1997) Residential Small Commercial
- Sales
- Working Project
- Superintendent
- Estimating
- Project Scheduling
- Accounting
Anncole Contracting Corp – President 1997-2014
Heavy Highway Civil Engineering Company / Focusing On Government Entity Contracts
- Estimating
- Project Scheduling
- Project Management
- Purchasing Agent
- Contract Negotiation
- Contract Procurement
- Accounting, Managed Bond Line
- Successfully Completed 40 Bonded Projects As Prime Contractor For ADOT and Various Government Entities
- Successfully Completed 70 Arizona Department Of Transportation Projects
- Successfully Completed 20 Projects For Various Cites, County Entities & College Systems
- Successfully Completed 12 Commercial Projects – Retail Shopping Centers, Parks
- Successfully Completed 1 Project For Department Of Navy
- Successfully Completed 2 TXDOT Projects
- Successfully Completed Bridge Overlay Project Houston Tx Road Toll Authority
Titan Development Groups LLC – Member 2014- Present
- Successfully Completed 4- Epoxy Polymer Bridge Overlays, 2 -Carbon Fiber Repairs Bridge Girders For TXDOT on Grand Parkway Toll Road, Various Concrete Injections And Crack Repairs
- Approved By TXDOT For Carbon Fiber Repairs Statewide
- Successfully Completed 60 LED Retro- Fit Projects, Arizona, Texas, Florida, Iowa, Illinois, North Carolina, Ohio, Colorado Minnesota, Missouri, Kansas, Kentucky, Mississippi, Alabama, & Wisconsin
- LED Retro-Fit Customers, International Paper, Delta Faucet, Sealy Mattress, Goodyear Tire, Winco Foods, Wincup, Tyson Foods, United Technologies, Baby’s Are Us, McLaughlin Associated Wholesale Grocers, Auto Body, Farmer’s Bank, Comtec Telecommunications, Transmatic, & First Credit Union
Project Management/ Consulting (2010- 2017)
- Control Estimating & Project Management for 10 Million Dollar Bond Line
- Estimated & Project Manager 20 Mile Pipeline In Nevada
- Project Manager, Contract Negotiation & Procurement- 8 Mile Waterline Colorado
- Project Manger – 2 Utah Department Of Transportation Projects
- Texas Parks & Wildlife Bastrop State Park Wildfire Recovery- Design, Estimated, Contract Negotiation, Project Manager 1.8 Million Dollar Design Build Project, Drainage, Erosion, Box Culverts, Drainage Re-alignment, Reinforced Concrete Pipe
- Bastrop State Park Soil Stabilization Post Wildfire 2.4 Million Project, Contract Procurement, Contract Negation, Project Manager
- Estimated & Project Manager 2.3 Million Bastrop County Road Rehabilitation
- Estimated & Project Manager 700K Las Vegas Water District Pump Station
- Estimated & Project Manager 11 TXDOT Projects
- Estimated & Project Manager City Of Mesa 9 Bridge Overlays
Our Trusted Suppliers
Associations
American Concrete Institute
The American Concrete Institute (ACI) is a leading authority and resource worldwide for the development and distribution of consensus-based standards, technical resources, educational programs, certification programs, and proven expertise for individuals and organizations involved in concrete design, construction, and materials, who share a commitment to pursuing the best use of concrete.
https://www.concrete.org/